Why it’s taking longer to build homes in Seattle
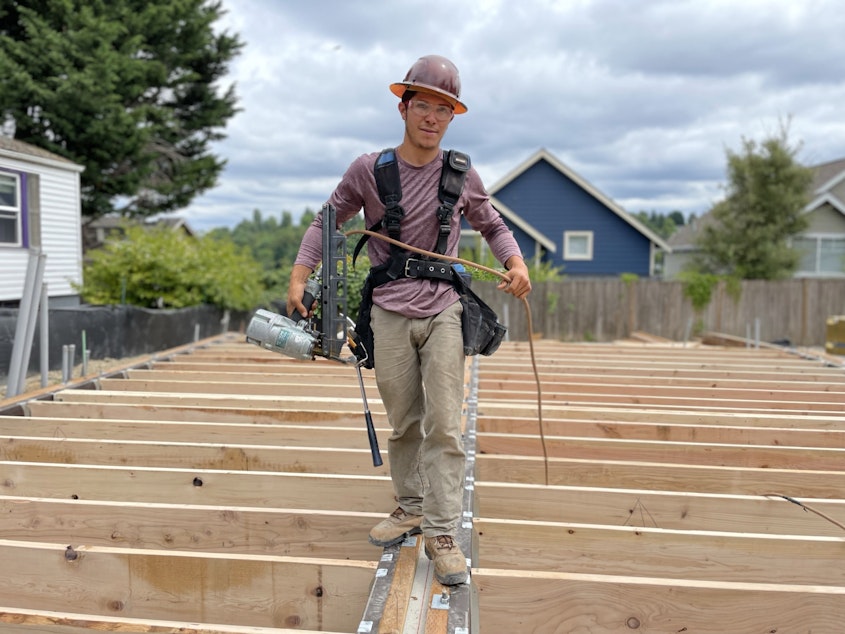
Home builders in the Northwest are working as fast as they can to build housing for all the people moving to the region.
Currently, there are 23,000 homes under construction in Seattle or about to break ground. But they’ve hit a snag. Or rather, a whole mess of snags. And those snags are slowing them down.
It’s early Friday afternoon on a leafy street in Seattle’s Madison Valley neighborhood. I walk to a site where there used to be a duplex. The contractor tore that down, and is putting up five three-bedroom townhouses in its place.
Worker Elio Gonzalez had just finished nailing together the floor joists. Then, he and his crew unplugged their nail guns and went home.
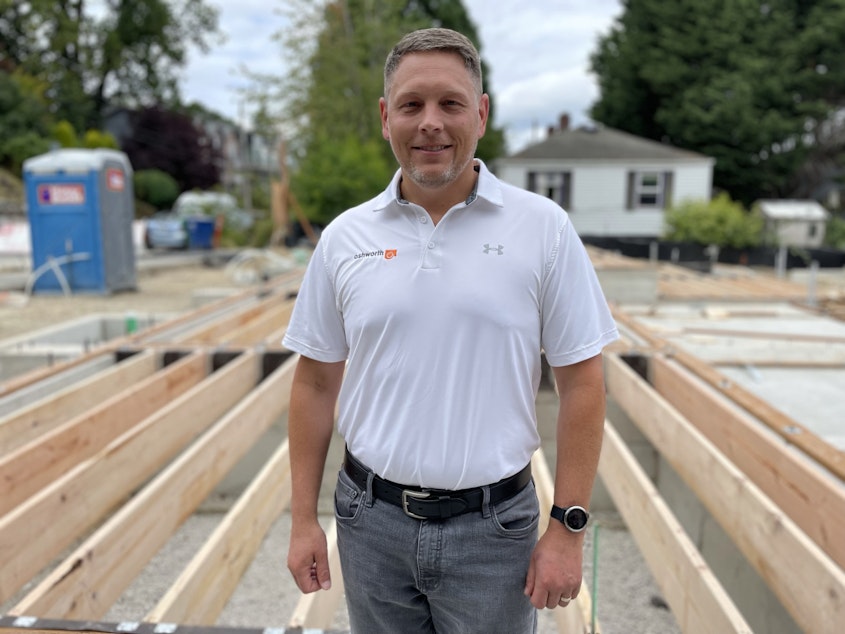
"As you can tell, we’re pulling off for the day," said Erich Armbruster, their boss and the president of Ashworth Homes. "Our next lumber load would be the first-floor walls, and it’s not here. And we can only go so far until we get our next load of lumber. "
What was the hang up?
"It’s just a lack of ability to get material out to jobsites," Armbruster said. "I honestly don’t know if it’s still a delay with the mills, or if it’s a delay at the yards, or a lack of drivers. I don’t know what the holdup is, but we’re now expecting this lumber load to come out on Monday, which, you know, is only a one-day delay, but over and over again, through the course of a job, delays the job quite a bit."
In Ballard, Trevor Johnson's company Blackwood Builders Group is finishing up some townhomes.
When Johnson needed washing machines for each unit, he reached out to his regular local suppliers in Seattle. But they didn't have any, and wouldn't for months.
His employees called all over the country, before finally finding some for sale in New York.
“I was shocked when they told me that," Johnson said. "I was like, 'What? Seriously?'”
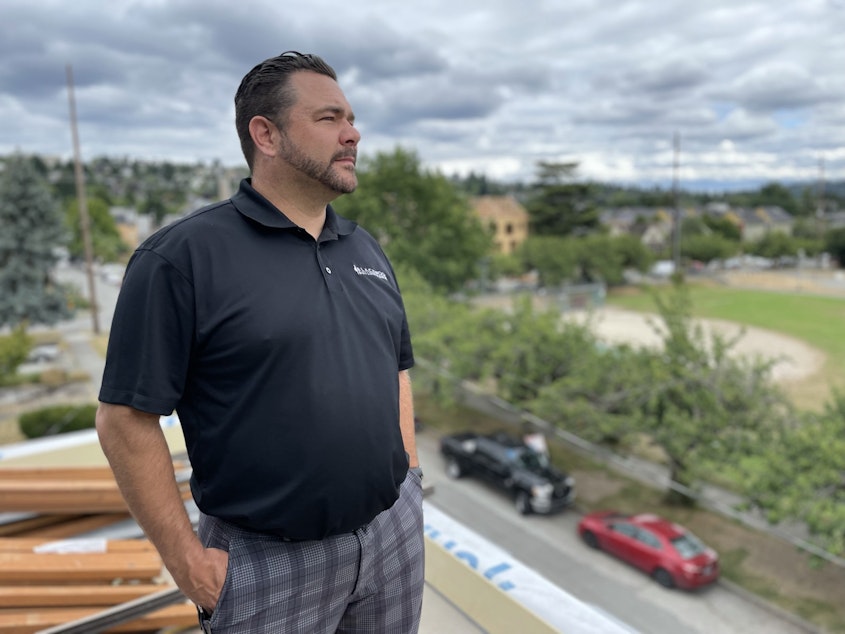
Engineered lumber, appliances and windows: These are just a few of the things developers used to count on to be available. But delays on these and other items have stretched out the time it takes to build townhomes in Seattle from 12 months to 18 months.
With a proper supply chain in place, contractors like Armbruster and Johnson buy properties with one, sometimes two homes on them for around a million dollars, and turn them into four to six homes listing for under $700,000 apiece.
Delays for contractors like these means less homes for the real estate market, which will lead to higher prices if demand remains high.
The reasons for delayed materials range from the pandemic to shocks to supply.
Lumber and appliances
Take wood, for example. Mike Dunn, CEO of Dunn Lumber says his industry is way behind on engineered lumber products, such as beams and plywood-like sheets (called oriented strand board) made from smaller scraps of wood, pressed together. Factories in Canada slowed down last year, but demand for plywood and other sheet products remained high last summer.
“Everybody was boarding up their storefronts, and that was truckloads of material," Dunn said. "So you get a hit to the supply side and you get a shock to the demand side ... We live in a just-in-time universe and it didn’t work this time.”
Many of the affordable appliances that go into apartments are made in Mexico. Those factories slowed to 25% during the pandemic, according to Jim Freedman, CEO of Metropolitan appliances in Seattle’s Stadium district.
But he says what really hurt the supply of appliances was the cold snap in Texas earlier this year.
There are a bunch of factories in Texas that make things like insulation and plastic. When the cold weather hit their hoses and pipes all burst and suddenly they stopped production.
“A lot of these companies had to completely redo their lines and get generators to be able to continue the process better," Freedman said. "It was very, very expensive for them. But in the meantime for them, there was no supply of that product going to the various refrigerator manufacturers to make refrigerators.”
That led to a severe refrigerator shortage.
The weather-related disaster in Texas hit the window industry too, which uses a lot of vinyl from Texas.
People to do the job
But there’s an even bigger problem facing the window industry, according to Rick Locke, owner of Windows, Doors and More in Seattle. It's a problem that's particularly apparent right now.
“I’m on the national board of directors for the national glass association – I just had a conference call this morning with our board," Locke said. "And one of the major issues that every single member of the board is bringing up for their regions and their segments of the industry is the availability of people. What do we do to attract people to the glass and window industry and work?”
All up and down the window supply chain, there's a shortage of people. People to make glass, people to assemble windows, people to drive trucks full of Midwest-built windows from the end of the train line in Oregon to the network of suppliers that feed windows to contractors throughout the Northwest.
From labor shortages to ships parked offshore because they can't get a berth at the port; from climate-related weather disasters to a lack of truck drivers, small delays are piling up and dragging down the pace at which our region's contractors build new homes. Some suppliers say it could take until 2023 for things to return to normal.
I asked Rick Locke, the window supplier, how we can fix these problems. He laughed.
“Well, I’m not sure it can be. You know? It’s not a thing that can be fixed. It’s a macro-economic phenomena that’s happening from a superheated world global economy.”
And when you’re running as fast as the global economy is and you trip on supply chain disasters like these, you hit the ground hard.