New infection-resistant, 3-D printed metal implants and the science power couple behind them
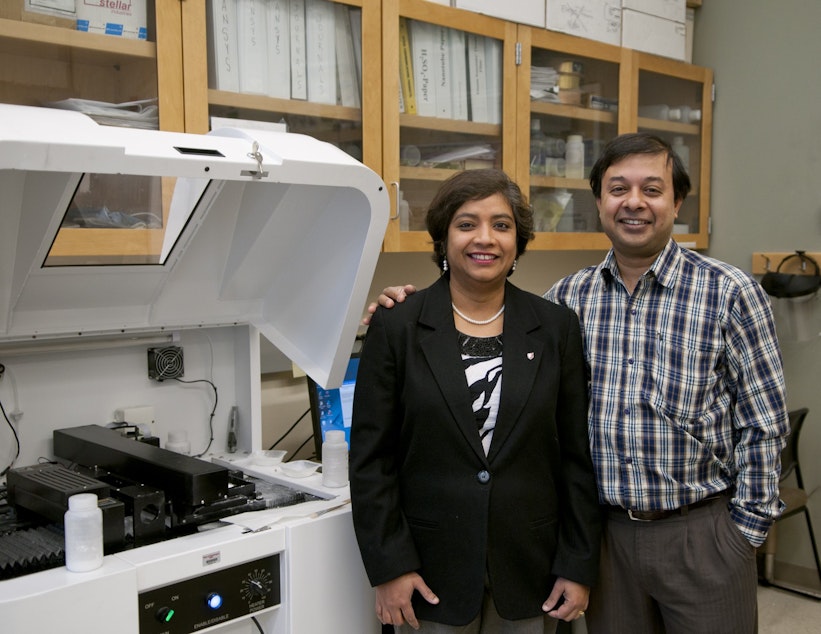
More than 100,000 patients with metal joint replacement implants get infections each year, and about half of them will need revision surgeries. These infections can be life threatening.
A new infection resistant, 3-D printed metal alloy implant could drastically reduce this number.
A
mit Bandyopadhyay and his wife, Susmita Bose, are professors at Washington State University’s School of Mechanical and Materials Engineering. Bandyopadhyay comes from an engineering background, while Bose researched chemistry. They started working on 3-D printed biomedical devices in the early 2000s.
This year, they created an infection resistant 3-D printed metal implant.
Bandyopadhyay said the implants that are currently on the market have not changed much. Traditional implants use titanium, a metal used in aerospace due to its durability and lightweight. Higher-end implants are coated with tantalum, a corrosion-resistant metal and encourages healthy cell growth as it has high biocompatibility with the body.
The couple wondered if there was a way to revolutionize implants while reducing infections.
Bacterial colonization of metal implants is one of the leading causes of their failure and bad surgery outcomes. Infection rates also increase when the original surgery is not planned, for example, like when a patient needs surgery for a bone fracture. These infections can be life threatening and can occur weeks or months after the surgery.
Bandyopadhyay and Bose looked at metals that have antibacterial resistant properties. One of those metals was copper.
“If you look at many door handles, they’re copper alloys, particularly in the hospital because it gives you an added protection,” Bandyopadhyay said.
But copper is not used in the human body often because too much copper can be toxic.
“We made sure the antibacterial agent we use does not release too quickly and become toxic,” Bose said. The new alloy for the implants “only kills the bacteria cells. At the same time it provides good biocompatibility so that good quality bone can grow,” she added.
The alloy uses 82% titanium, 10% tantalum, and 3% copper. The research on this new alloy was conducted over three years, both in the lab and in animal models.
“There is nothing like it, so we can really call it a multifunctional device,” Bose said.
They aim to increase the bacterial death rate from 87% to 99%, without compromising the tissue integration.
The couple also studied the material’s wear to ensure that the metal ions from the implant will not wear off and move into nearby tissue and become toxic, they said.
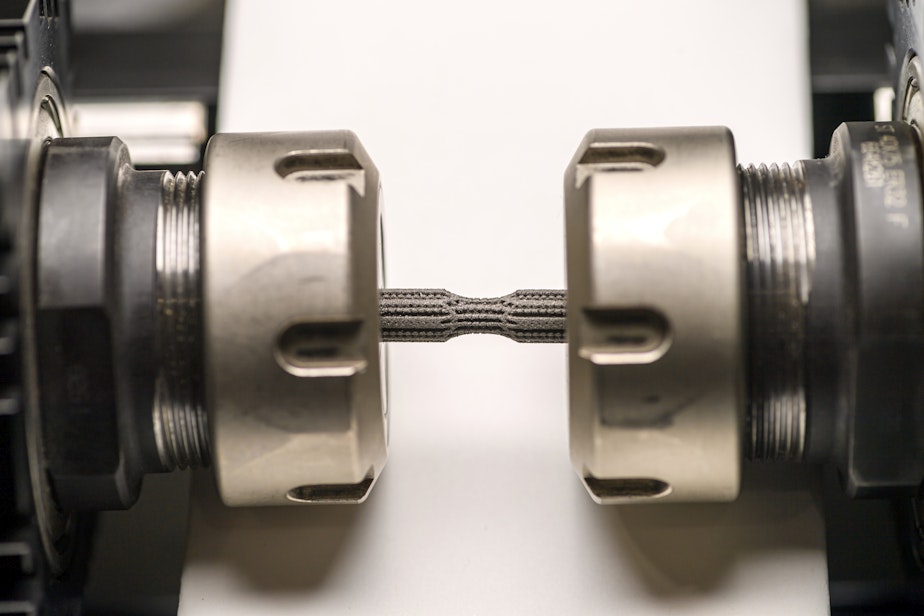
This new alloy can kill 87% of the bacteria that causes staph infections in laboratory tests, according to Bandyopadhyay.
3-D printing implants is also important for today’s world, Bandyopadhyay said.
“It helps you do two things: on demand manufacturing and customized manufacturing. You are not making a large number and storing them. You can also customize it, from a knee implant to a spinal implant to a dental implant,” he said.
Bandyopadhyay and Bose’s research was published in the November edition of the International Journal of Extreme Manufacturing. WSU’s Office of Commercialization has filed a provisional patent.
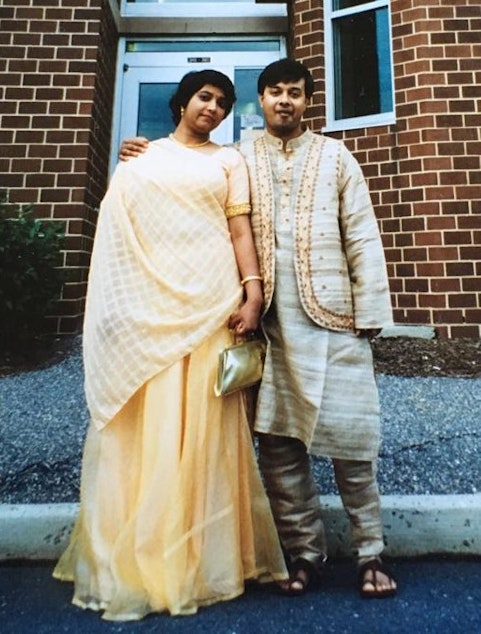
Working together hasn't always been seamless for Bandyopadhyay and Bose.
The couple met at Rutgers University through Bose’s roommate over Chinese food. Bandyopadhyay said working with a spouse was harder in the early days, “but with time, you appreciate things differently.”
Bose joked that she used to say, “If you can work with your spouse, then you can work with anybody in this world because that’s the hardest thing on earth.” But that means they can celebrate their success — and eat Chinese food — together.
